Low energy consumption in high demand
Paint shop is still a key area
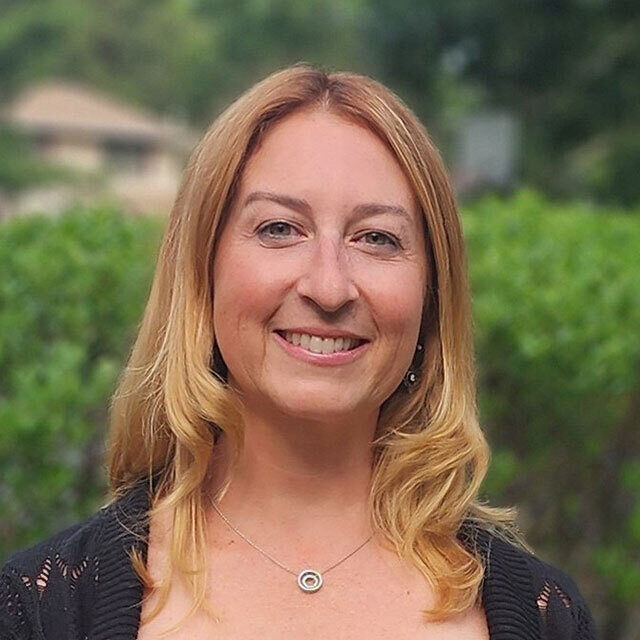
Alisha Bellezza
Vice President of Global Automotive Coatings for PPG
Alisha Bellezza, Vice President of Global Automotive Coatings for PPG sees reducing carbon emissions as one continuing trend in automotive coatings
Do you see developments that could lower energy consumption for automotive coatings?
Through continuous research and development, PPG provides multiple technologies to our customers to lower energy consumption throughout the entire automotive coatings production process. Along with the rise in production of electric vehicles, the automotive industry continues its focus on sustainability in manufacturing operations. We anticipate that sustainability and reduction of the carbon footprint in automotive manufacturing will remain a key trend throughout 2024. Approximately 70 percent of total energy consumption at automotive assembly plants takes place in the paint shop. We have and continue to develop industry-leading sustainable innovations that support our customers' sustainability and improve their productivity. In 2023, we unveiled our suite of electrocoat products with an expanded cure window which enable the customer to reduce oven temperatures or allow for heavier metal mass without making additional capital investment. Since structural body shop adhesives are also cured in the electrocoat oven, PPG has developed an expanded cure window structural adhesive with the temperature cure profiles similar to the electrocoat product. PPG continues to be a leader in the B1:B2 low-energy compact topcoat paint process for automotive OEMs. This technology has demonstrated up to a 20 percent reduction in energy intensity and carbon footprint in the OEM paint shop decorative coating process. Furthermore, PPG has two products which enable our customers to shut down their decorative sealers oven and, therefore, achieve additional energy and carbon emission reductions, representing up to an additional 5 percent reduction in energy intensity and carbon footprint in the OEM paint shop decorative process.
What are the hurdles to transitioning to more waterborne systems in automotive coatings?
We offer everything from waterborne and solventborne primers, basecoats and clearcoats to powder primers and scratch-resistant ceramic clearcoats. PPG is continuously developing smarter solutions that keep us at the forefront of product compliance, sustainability, and innovation. One of the ways we do so is through lower volatile organic compounds (VOCs) coatings, including waterborne coatings. We have a vast and growing portfolio of waterborne coatings that meet environmental regulations across the globe and are designed for a wide range of surfaces, products and industries, including automotive manufacturing.
VOCs are pollutants to the atmosphere and are abated by our customers with thermal oxidizing equipment. However, burning VOCs emits carbon dioxide and contributes to the CO₂ emission of our customers.
That is one of the reasons manufacturers may make the move to our waterborne solutions. In certain process set-ups, waterborne coatings may also require more energy to be applied and cured compared to solvent-based solutions. A thorough calculation that considers all the process steps – application, curing, and thermal oxidation of the VOCs – is required to determine the best option, waterborne or solventborne. In addition, PPG has made advancements in appearance and functionality of powder coatings, making this technology a viable alternative. Powder coatings are a sustainably advantaged technology. Unlike liquid paints, powder coatings contain no solvents and release little or no amount of VOC into the atmosphere. Powder coatings are cost efficient and can be reclaimed during application, offering more than 90 percent transfer efficiency, and have minimal impact to the environment as no solvents are used for clean-up and no hazardous waste is generated.
What impact do you expect from trends like electric cars and self-driving vehicles for the automotive coatings industry?
The automotive industry is in the midst of a significant shift to electrification, and the development of autonomous vehicle (AV) technologies continues. Our innovative paints and coatings will play a leading role in this transition and will advance the technology to improve driver safety, assist in meeting sustainability goals, and drive productivity for our customers. Our broad-based materials expertise and ability to tailor critical properties touches virtually every area of battery design and construction. Along with protecting and beautifying all vehicles, including electric and autonomous, PPG helps OEMs as well as battery and component manufacturers accelerate the development of tomorrow’s automotive and commercial vehicle energy storage solutions. And, we continue to adapt what may be considered traditional coatings to meet the CASE trends, such as managing accelerated light-weighting, improving ADAS and AV sensor performance, and improving visibility, to name a few. To meet our customer’s needs, we recently opened a battery pack application center. This site features a full range of capabilities to test the application of PPG coating technologies, materials and systems for electric vehicle battery packs, allowing customers to accelerate the development of EV technologies throughout the global automotive industry.